We make all products, from yarn to finished garment, at our own factory right outside of Bergen, Norway. And we want to keep you in the loop, by sharing everything there is to know about our processes, as well as welcoming you for a visit. This is how it’s done.
First floor power
At Ivar Aasgards vei 1 in Ytre Arna, the production is divided in two stories. On the bottom floor, we knit. Yarn arrive from our suppliers, in different qualities and colours - under strict quality check by Silje, our Knitter in charge. She is a perfectionist when it comes to colours. We keep at least 90 shades in stock at all times, to enable an agile production even if lead times on raw materials are long.
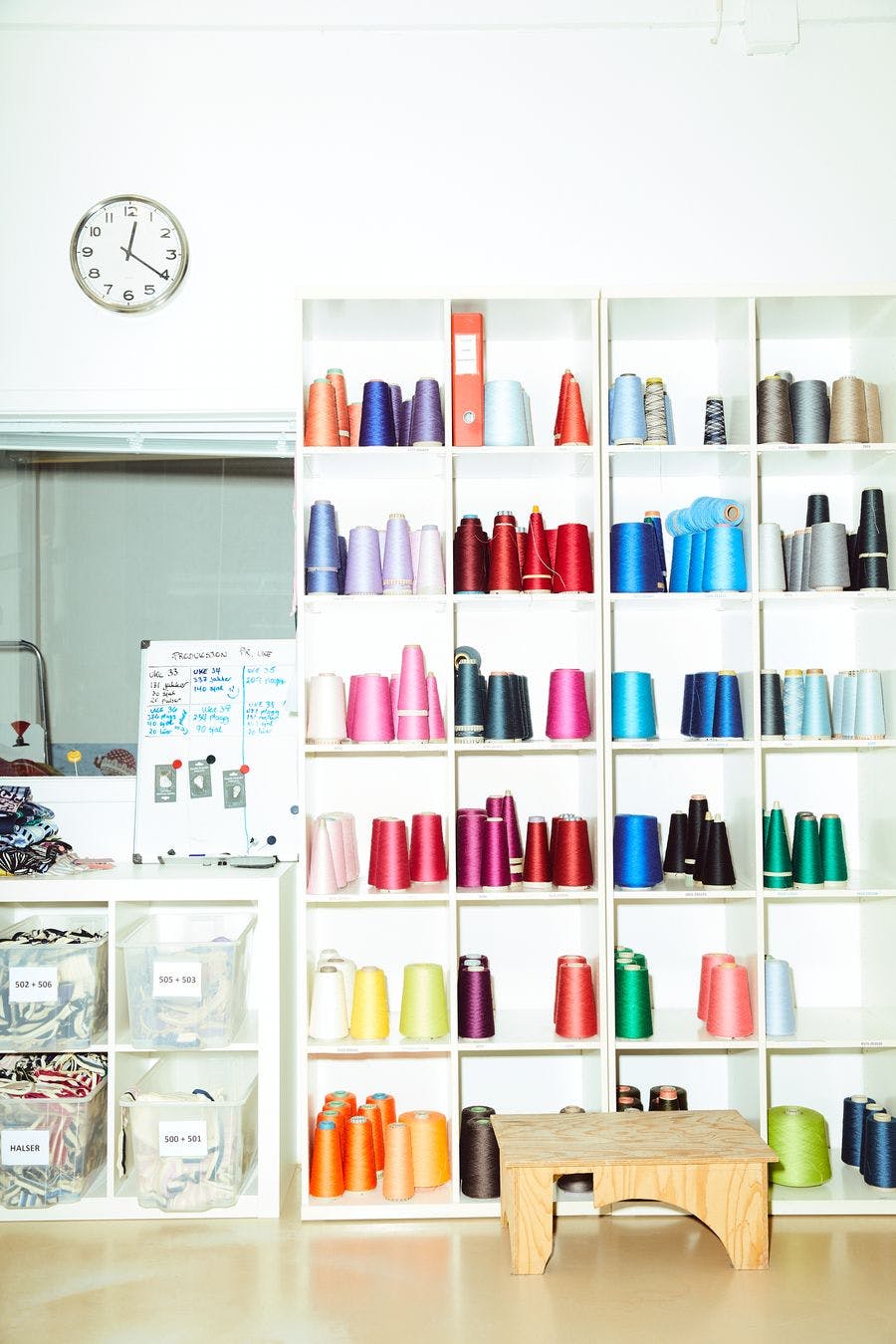
We have about 20 knitting machines in operation, of different types used for different quality yarns and different type of products. Upon a production order, our knitters follow a precise description for each garment, with yarn details, machine to use, machine settings and digital pattern files, along with measurements to match once the first panel of each batch is ready. A production batch at Oleana can be anything between five and twenty garments, or on rare occations even just the one jacket. When all panels, details and trims for one batch is ready, all knitted bits go through a steaming process, and then a first quality control before being packed on a trolley and sent upstairs.
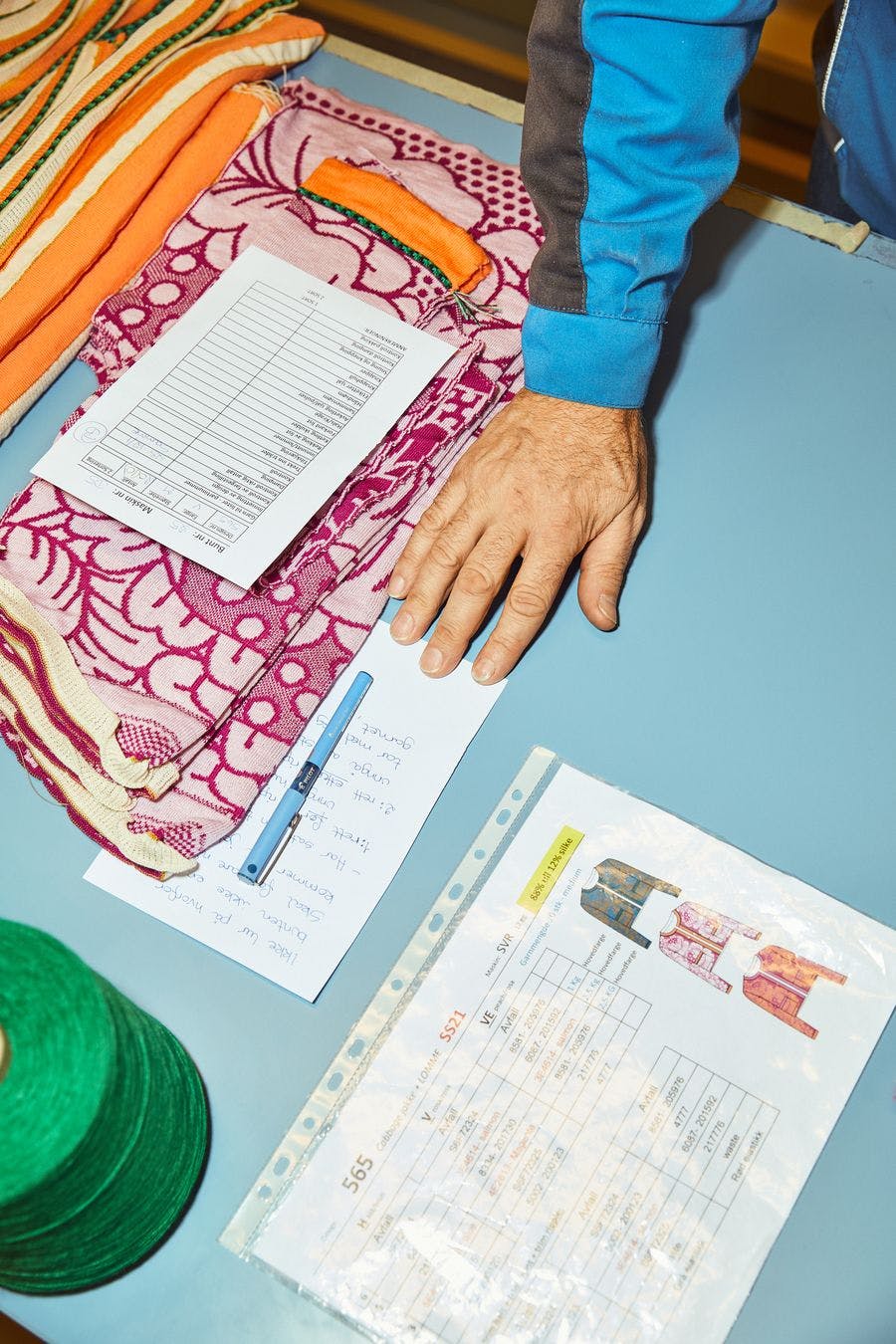
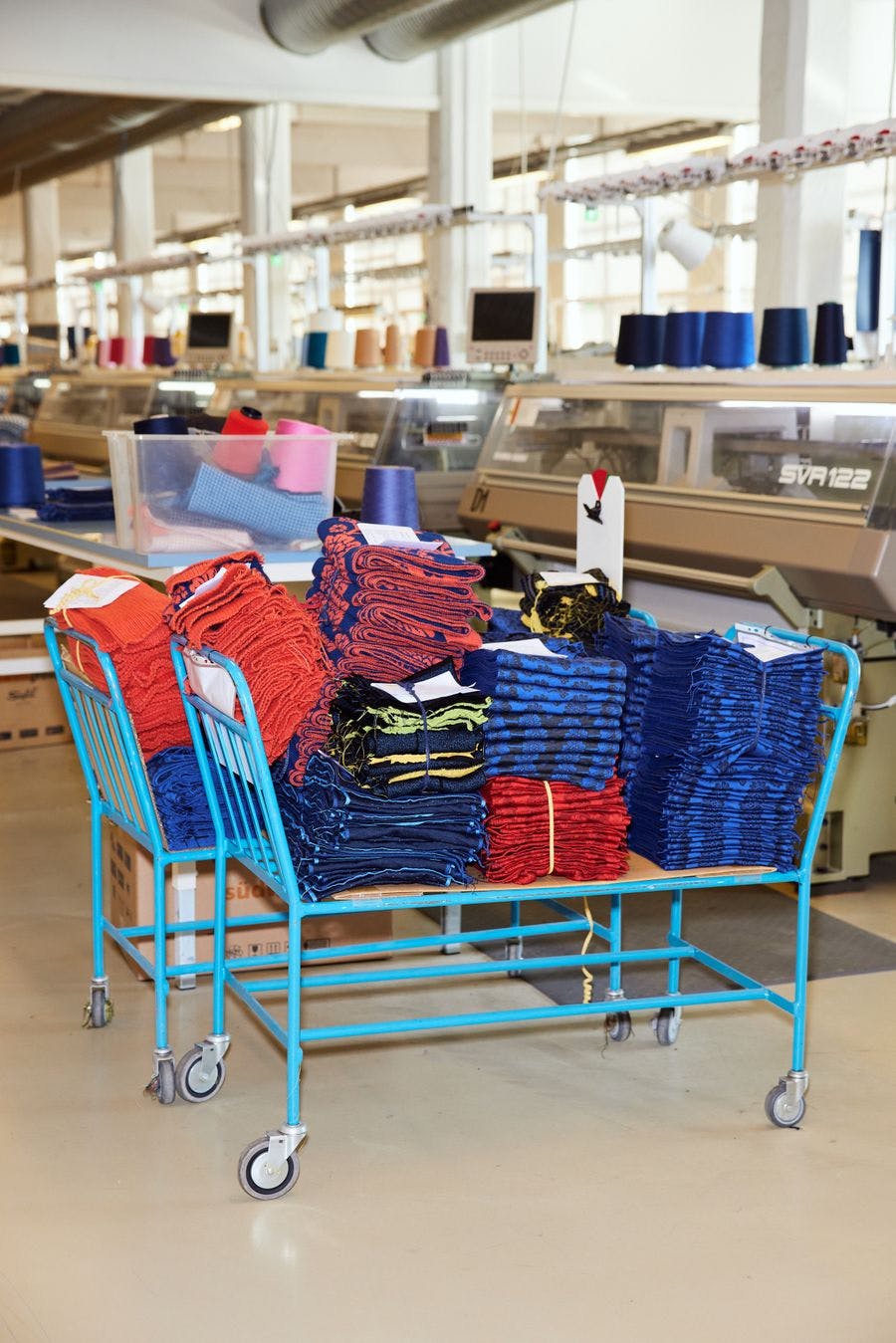
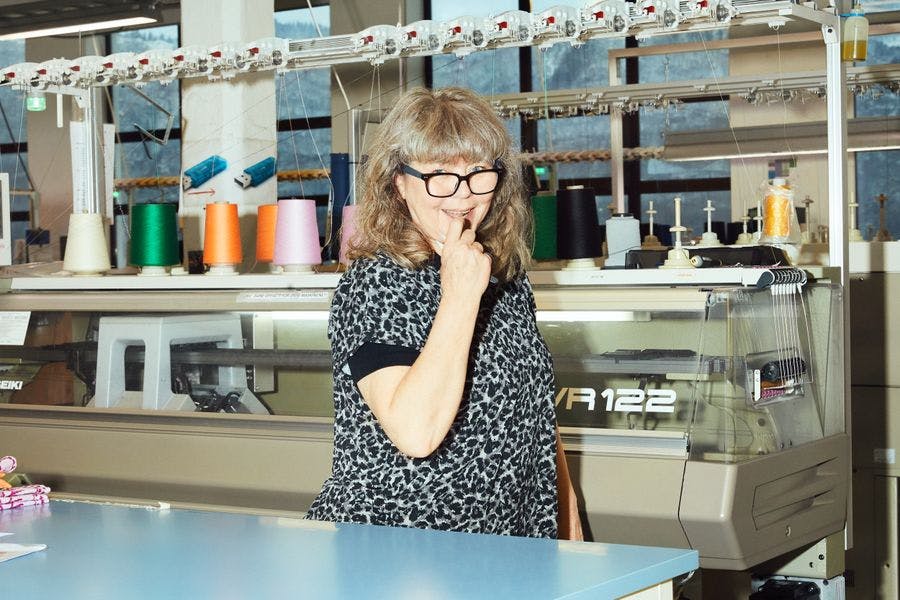
On the second floor
Up one flight of stairs, the knitted panels are crafted into finished garments. The process of doing that is different for each style. The majority of our propducts have an element of linking. It’s an intricate and time consuming process, but essential to achieve an exclusive and durable garment. Our skilled linkers attach trims and details, like button bands or collars, by manually catching each loop of the knit onto a small peg and then sewing a chain stitch seam. The seam locks open stitches and attaches the detail, without any excess fabric or seam allowances. With a fine-tuned and regularly quality checked linking process, the seam will come out exactly as stretchy as the knitted garment itself, reducing the risk of seams ripping immensely. We also use more conventional sewing machines to assemble other parts of garments, like when attaching a sleeve for example.
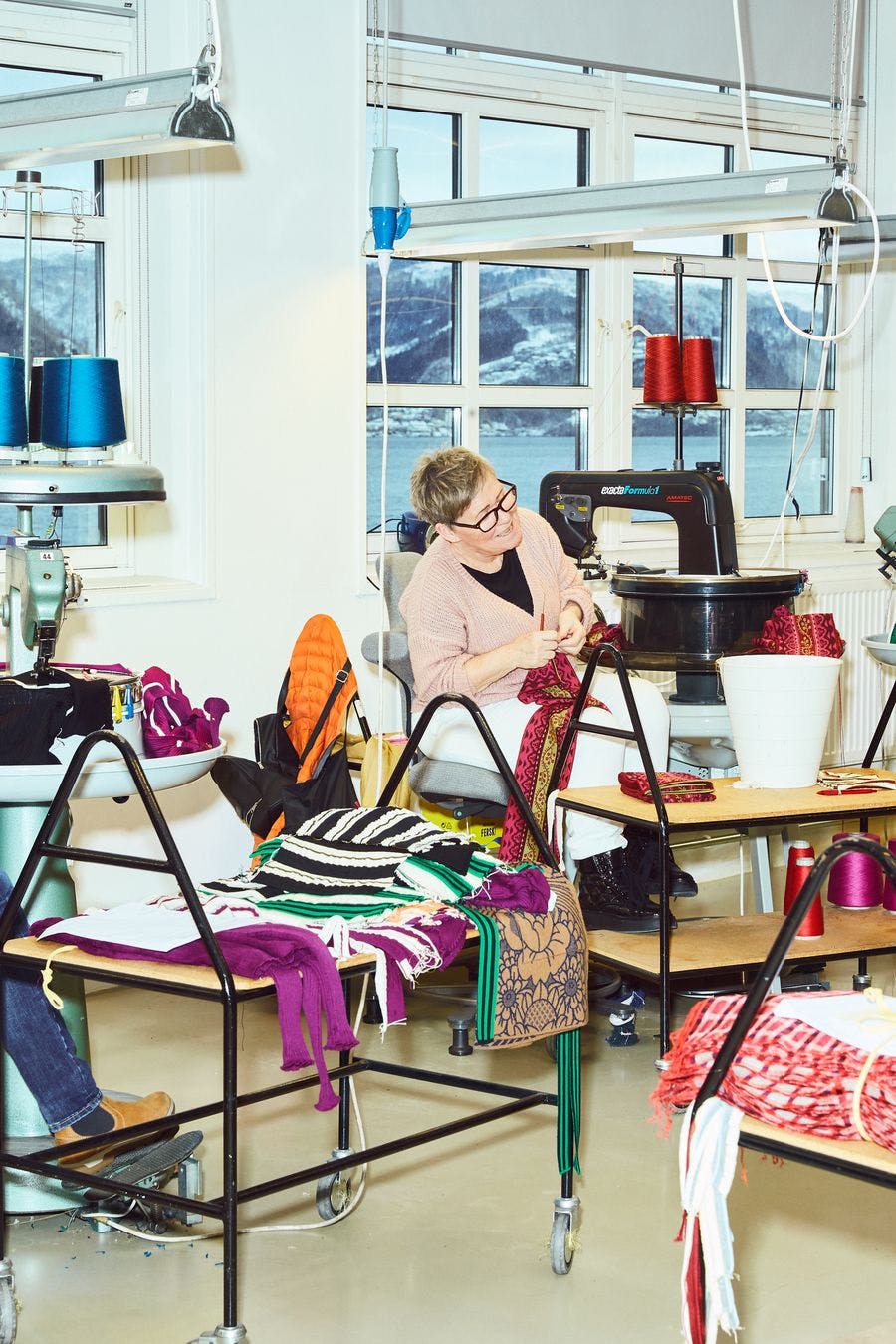
At the second floor we also keep special machines to attach buttons, and our great button library, with hundreds of different type buttons, for different styles. Our tailoring department make trousers, skirts, and dresses from woven fabrics, as well as our iconic blanket coats.
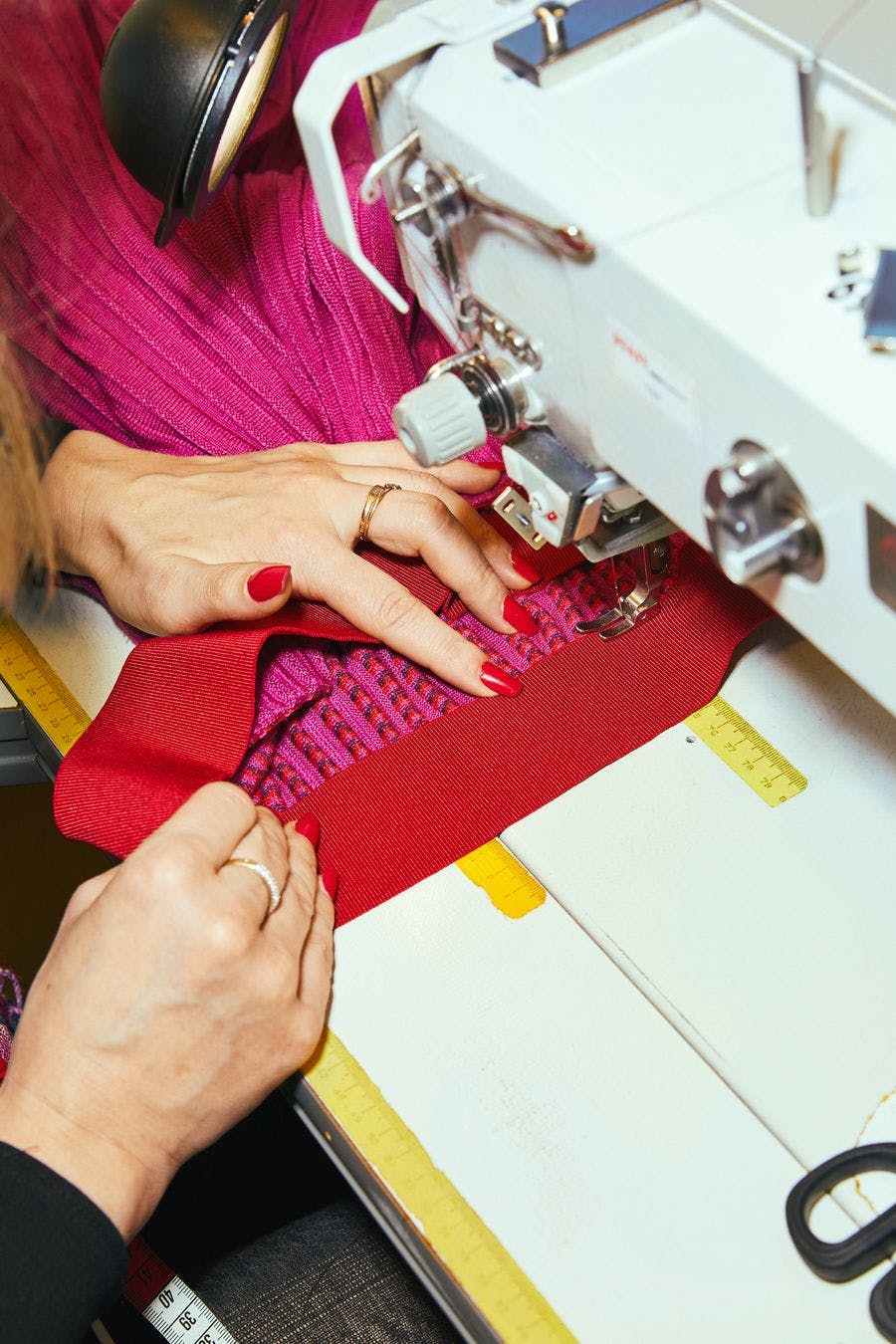
To achieve a soft and relaxed knit material or garment, we use a lot of steam. Some garments are steamed by hand, using a steam iron, and some on our big steam bed – once, or several times during the process. Last, but not least, the garments are quality checked one last time, before getting labeled, folded and packed, and sent upstairs to the stock room.
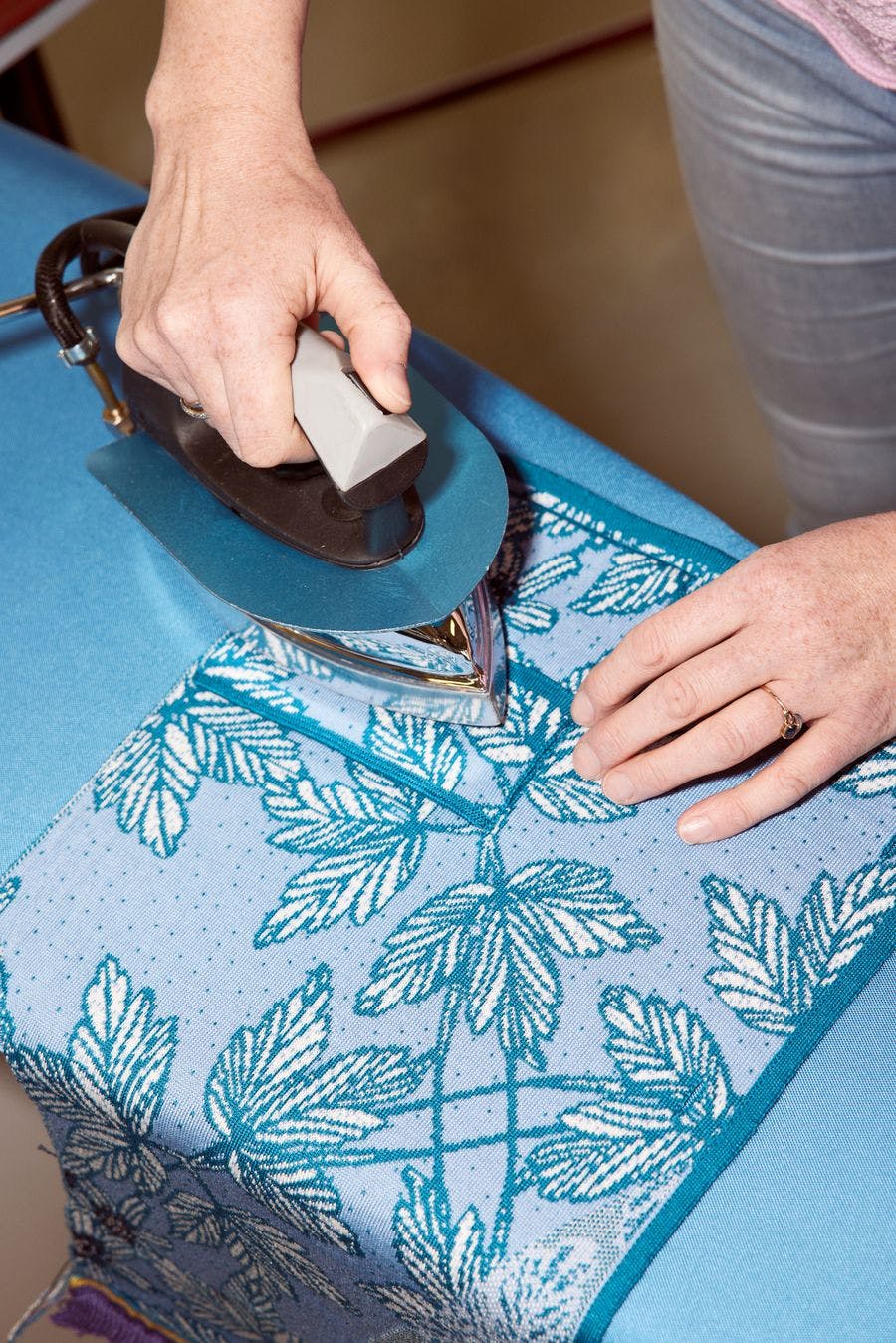
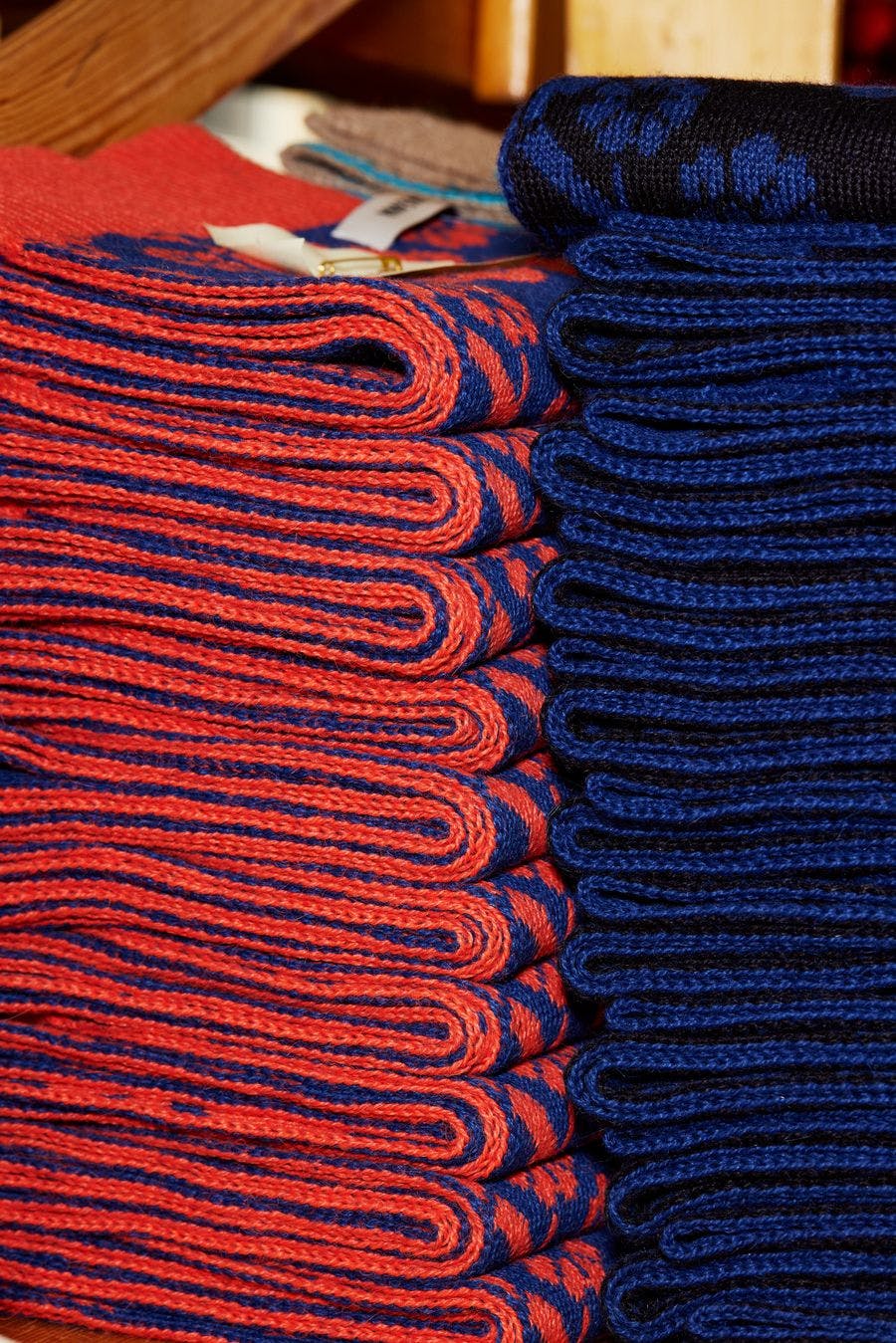
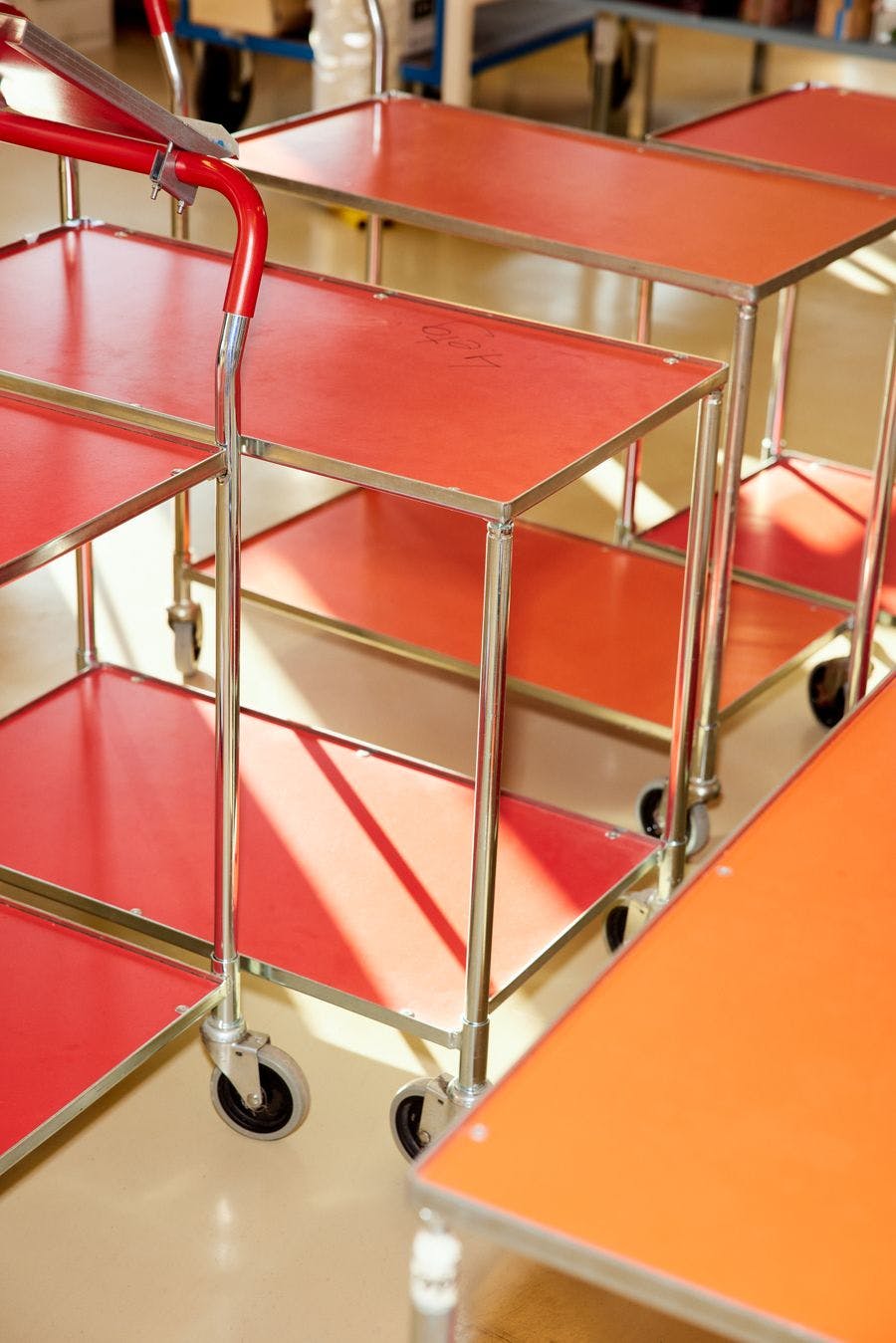
Stock room
On the top floor of the factory, we try to keep stock of all styles, in all sizes, always. And that’s not just for this season, but for as long as a style is in demand. This philosophy of ours, means that we still produce garments first designed 15 years ago. A style, for us, is never just for one season. There is no end of season-sale, or anything last season.
At the stock room, Vaida is in charge. She keeps track of shipments through our web shop and to retailers. She will send that production order back to the first floor, for another loop.